Moulds are the special tools used to make products from different materials. Whether you’re looking to manufacture metal or plastic, you need the right molds for your project. Read on American Plastic Molds for more information.
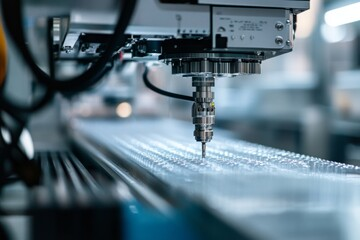
Choosing the right type of mold can save you time and money in the long run. Depending on your project, you might need a family mold or hot runner.
Plastic injection molding is a common manufacturing method for producing many products. It involves injecting molten plastic resin into a mold cavity to form the desired shape. The high pressure used in this process can allow for the inclusion of detailed features and complex geometries. It also allows the use of multiple plastics, including blends of different materials for specific physical or mechanical properties.
The injection molding process is most commonly used for thermoplastic polymers, which can be repeatedly melted and solidified without degradation of their physical properties. The most common type of polymer in the injection molding industry is polyethylene (PE). Other popular thermoplastics include polypropylene (PP), polystyrene (PS), and acrylonitrile butadiene copolymer or ABS plastics. A variety of additives can be included in the resins to modify their performance characteristics or for environmental reasons, such as biodegradability or food safety.
Once the plastic is injected into the mold, a high holding pressure must be maintained to compensate for shrinkage of the material. This pressure is known as the clamping force or tonnage and can be influenced by the size, thickness, and material of the finished product. It is also influenced by the injection pressure and flow characteristics of the molten plastic, with thicker and more viscous materials requiring higher injection pressure to maintain a consistent volumetric flow rate.
During the injection molding process, the sprue bushing seals tightly against the nozzle of the injection barrel and directs molten plastic into the mould image areas through channels that are machined into the A and B plates. These channels are referred to as runners. The gate is an opening in the runner that directs the molten plastic into the mould cavity, and its type, location, and design can influence cosmetic appearance, part dimensions, and warping.
The injection molding process can be improved by lowering the injection temperature, increasing the holding time, or both. These actions can reduce or eliminate the formation of sink marks on the surfaces of molded parts, caused by differences in cooling rates between thicker and thinner sections. The resulting marks are unattractive and may indicate added stress within the part.
Vacuum Injection
Vacuum injection is a molding technique that uses a hollow space in the mold to assist with creating a solid plastic product. This method of molding allows for faster production of parts and the ability to create a high volume of identical and dimensionally consistent products. It is often used with thermoplastics, such as polyethylene and polystyrene, which are easy to work with and have good flow properties.
When a plastic part fails to meet specifications, it is often because the process isn’t finished or there are issues with the quality of the plastic used. Depending on the problem, it may require a re-design of the plastic or a change to the injection machine. It can also occur because the material isn’t suited for the product’s intended use or because of issues with the mold itself.
The part may also be subject to thermal decomposition. Thermal degradation is a series of reactions that cause a chemical to decompose through discoloration, distortion or localized destruction of the surface of the plastic. This is typically caused by overheating or exposure to high temperatures.
Injection mold defects can affect the appearance, durability and structural integrity of a plastic part. They can be caused by a number of factors such as uneven cooling, inadequate injection pressure and mold design. It’s important to understand the causes of these defects in order to prevent them.
Some common injection molding defects include vacuum voids and burn marks. These can be caused by a number of different reasons such as thick walls in the mold or insufficient injection pressure during the transfer phase. The injection pressure should be increased to allow the molten plastic to transfer into the cavities quickly and effectively.
Other issues with injection molding include flow lines and wavy surface markings. Flow lines are a result of the melted plastic attempting to cool and solidify too fast, resulting in the uneven formation of plastic. This can be corrected by reducing the injection speed or using a cooler-temperature resin.
Lastly, a product may be subject to shrinkage. Shrinkage is a normal part of the cooling process but can be difficult to overcome when working with a highly-compliant material such as nylon or a tough, fatigue resistant thermoplastic like propylene. A re-design of the mold or the injection machine can help reduce the occurrence of these types of defects.
Rotational Moulding
There are many different ways to manufacture hollow plastic products, but rotomolding (or rotary molding) is one of the most common and efficient methods. The process is used to produce a wide range of products, including toys, road cones, car armrests, and boats. It is also ideal for constructing durable, weatherproof items that can resist impact, corrosion, and external elements.
The rotomolding process involves heating up and slowly rotating a hollow mold filled with powdered plastic, usually polyethylene. This allows the heat to melt the plastic and form it into the desired shape of the product. Then, the molten plastic is cooled so that it can harden and become solid before the operator removes it from the mold.
This method is particularly useful for producing hollow construction items because it doesn’t require the use of any additional materials, such as sprues and runners. This also means that it produces less waste in production than other types of molding, such as injection molding.
However, rotomolding is not without its drawbacks. For example, it takes a long time to heat the mold and cool it down again. This can result in longer cycle times and increased costs for the manufacturer. In addition, it is only suitable for the use of certain types of plastic that can be turned into a fine powder with high thermal stability.
Another disadvantage of rotomolding is that it does not generate the same amount of pressure as other processes, and this can lead to cross-sectional distortion in the finished product. The solution to this is to ensure that the cooling of the plastic is carefully controlled so that it does not warp and change dimensions.
The final advantage of using rotomolding is that it can be used to create high-quality plastic products that have excellent surface details, such as color and texture. In addition, it can create a highly uniform wall thickness, which is important for the durability of a product. It is also possible to make a number of different styles of products using this method, thanks to the versatility of plastic materials and the flexibility of the rotomolding process.
Casting
Casting is a process in which liquid metal takes the shape of a mold, producing a finished product. This is distinct from injection molding, which uses high pressure to inject molten materials into a mold to produce a solid object. It can be used to manufacture products from a variety of materials, including plastic and metal.
Creating a casting begins with the creation of a pattern, or master pattern. This is a reusable or sacrificial model of the final part that will be used to form the cavity into which the molten metal will pour. Depending on the type of casting, the pattern can be made from a number of different materials such as wax, sand or plastic. It can also be produced using a tool, which is a reusable metal portion commonly found in processes like die casting.
Once the pattern is created, it is surrounded by a mixture of sand and resin to create a single-use mold. The mold is then filled with molten metal and allowed to cool. Once the cooled casting is removed, it is cleaned and polished.
The casting process can be used to create a range of different parts, but is particularly well suited for larger metal components that require a great deal of strength and durability. This includes items like air ducts, machinery components and automotive parts such as engine blocks and heads.
Another benefit of casting is its versatility in design. This is possible because the casting process can be used with different types of metals and alloys, including ferrous and non-ferrous varieties. It is also possible to cast a wide variety of shapes and sizes, from simple hollow tanks and containers to decorative statuettes and figurines.
Other benefits of the casting process include its speed, efficiency and accuracy. The rapid cooling time of the molten metal allows the casting to be produced in a short amount of time, and this reduces production costs. It is also possible to achieve a high degree of dimensional accuracy, which is important for complex designs. This is because the foam patterns that are surrounded by the sand-resin mixture vaporize as they are heated, leaving behind a cavity into which the molten metal can flow and solidify, replicating the original design precisely.